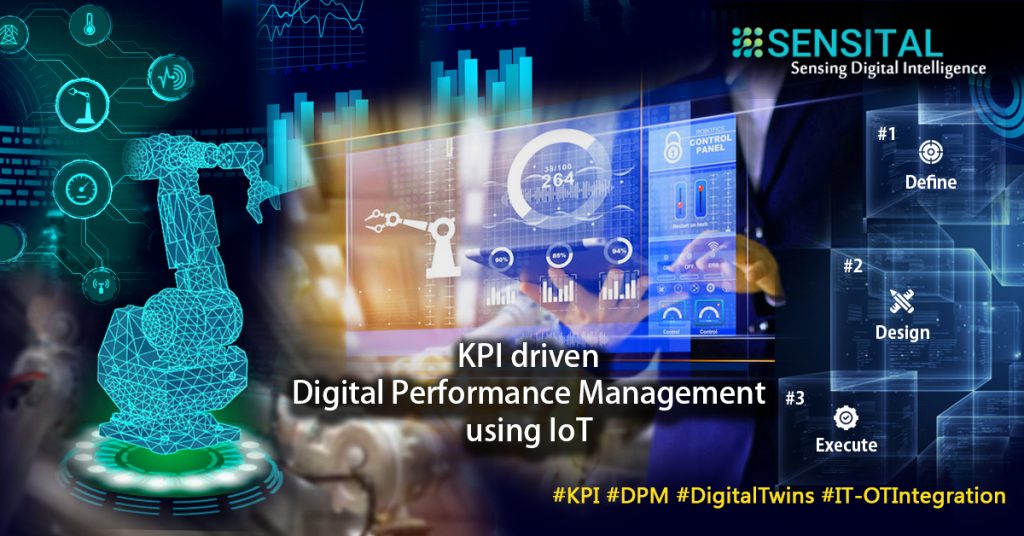
IoT technology and the ecosystem built around it has given us real-time insights into the physical or operational world. Specifically, IT-OT integration has allowed us to monitor various aspects of any equipment, machine or an operational process and extract meaningful data from different states of these operational technologies. It has opened doors that did not even exist earlier and has given enterprises a variety of creative options to leverage IoT to extract operational efficiencies.
Digital Performance Management
One such new application of IoT that has emerged is Digital Performance Management (DPM). There are a variety of classical definitions of DPM, but the one we focus on here is the meaning of DPM in the context of IoT and I define is as follows – DPM is the digitization of the management of any operational asset or process from the perspective of its performance. For example, DPM would provide one with insights on the performance of a CNC machine, a transformer in a power grid or the extrusion process in a manufacturing plant, etc. The kinds of insights provided are contextualized and dependent on the asset or the process being managed.
Performance Management is more than just Monitoring
What makes DPM different from IoT driven asset performance monitoring is that DPM takes the notion of IT-OT integration for asset or process monitoring two steps ahead and actually attempts to improve the performance of the asset or process being managed.
Now, there are a few things that are needed to make an IoT based monitoring capability into a proper digital performance management solution. The usual suspects that make the list are real-time data collection from your operational technology, followed by data analytics. And we know the role IoT plays here in terms of facilitating data collection built using real-time sensor-ized data broadcast from your operational technology. However, the key to true performance management lies in other capabilities that an IoT ecosystem needs to offer.
Operational Information Flow Modeling
To be able to truly understand and appropriately process data coming from any asset at any point of time, it has to be contextualized. We do this by also simultaneously capturing data coming from other sensors tied to assets up and down the operational process chain and superimposing the flow of information through that operational process. This operational information flow model is critical for the contextualization of the information coming from the various sensors and devices.
Digital Twin with KPIs
Modeling the operational information flow, identifying key performance indicators and defining optimal-state values gives us a baseline to measure against. Comparing the data coming from the actual information flow at any time with this Digital Twin will generate the insights needed to determine if the performance of assets individually and within the context of the operational process is as desired or if anything needs to be changed. This change may be needed either on the asset itself or anything else upstream or downstream that may impact its performance.
Initiating a Control Action
Knowing that something is not right is obviously important, but imaging being able to fix it – now that’s true performance management. This is where bidirectional communication between the IoT technology and the operational sensors and devices comes into play. Information must flow not just from the sensors and devices to the IoT technology, but instruction based on intelligent analysis decisioning has to be pushed out to these devices. This instruction will help us “digitally manage the performance” of the operational asset or the process, and through it the entire operation, like a factory or a power plant or an oil rig, etc. It allows us to close the loop and drive continuous performance management and improvement, very similar in paradigm to what one may see with Deming’s cycle or any Six Sigma based quality control process.
For IoT based DPM to be successfully applied in an enterprise, certain practical challenges associated with IoT also have to be overcome. Some of these are technological complexities slowing the adoption of IoT and others are caused by the proliferation of technology to fulfill the need for IoT.
Digital Performance Management using IoT in 3 Steps
An IoT platform that supports everything from device discovery and connectivity to information flow modeling and integrations is key to the success of enterprise digital performance management. Sensital’s iBOTics IoT platform incorporates the key components of Digital Performance Management (contextual information, digital twin with KPIs, control action initiation) in its 3-step process:
- Define – your assets, data types & formats, communication protocols between various devices and between devices and your Information Technology.
- Design – your real-world information flow model, including any data transformations and integrations with enterprise systems.
- Execute – your interactions and trigger real-world actions in your OT or IT, based on triangulated information available at the right time and measured against the baselined KPIs.
By applying this no-code, easy to configure 3-step process, any enterprise can launch its Digital Performance Management program and generate measurable savings and predictable Return on Investment. If you wish to learn more on how you can launch your DPM initiative using Sensital’s iBOITics platform, please feel free to reach out, and we will gladly share our experience with you.