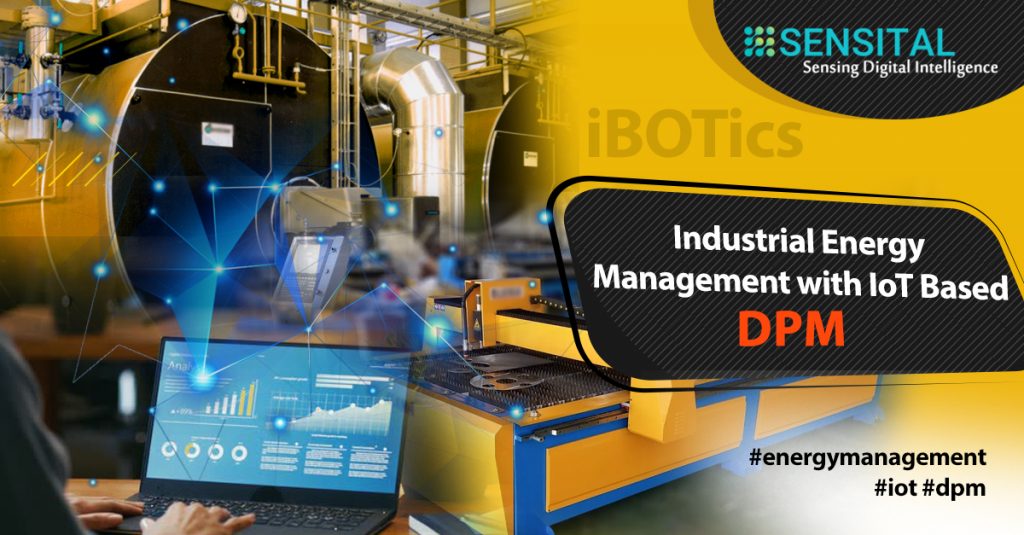
Energy costs are typically the highest indirect expense in the manufacturing industry. A study conducted by the Australian Government showed that HVAC systems alone make up for about 40% of that energy expense. Manufacturers pay billions of dollars in wasted energy costs every year just in running their air compressors. With a strong focus on Net Zero and the environmental costs of energy consumption, manufacturers have to think about operational costs management as well as their carbon footprint. By improving the efficiency of their operational assets manufacturers can directly impact their bottom line, improve margins and reinvest these savings in creating competitive designs and products.
Opportunities for Industrial Energy Management
HVACs, boilers, and air compressors are some of the typical equipment one would see in any manufacturing plant. Several factors, including poor calibration, lack of timely maintenance or unnecessary use, etc. contribute towards the inefficient operations of such equipment. By monitoring certain KPIs for these assets, we can determine if the asset is performing at a peak or if there is performance degradation or energy loss in the process.
For example, let’s look at one of these components, the compressed air network, in some more detail. Compressed air is used in manufacturing plants in various ways to drive pneumatic tools and machinery. While air is free, a significant effort and energy goes into compressing it and delivering it to the various end-points that tools can fit into or connect to. Performance of the air compression network depends on the ability to maintain air pressure till the end point, of course, but also on the cleanliness or air, moisture levels, and importantly, the temperature of the air being compressed and transported. This means measurement and maintenance of air temperatures through the network, checking for leaks and undesirable pressure drops, moisture levels in the air, etc. is critical for the efficient functioning of the equipment.
In addition to these areas of performance measurement, one also must ensure that the air compression system is available and running only when needed and is producing the right amount of compressed air for the right consumption end-point. This prevents damage to the machinery and avoids excessive energy spend to generate air pressure that has to be let out through a release valve.
Similar controls, measures, and checks can be applied to HVAC systems, boilers, humidifiers, etc. as well.
IoT based Digital Performance Management
One such highly effective way of managing energy costs in manufacturing plants is applying IoT based Digital Performance Management principles. I talked about DPM & IoT in one of my previous blogs in more detail, but I will briefly repeat what I mean by DPM here – Digital Performance Management is the digitization of the management of any asset or a process from the perspective of its performance.
So, how do we apply IoT based DPM to extract operational efficiencies in terms of energy savings in a manufacturing plant. Let’s go back to our example of the compressed air network.
Pressure drops: We know that pressure drops can happen in different areas of the network for a number of different reasons. They could be caused by higher pre-pressurized air temperature that cools after compression while moving through the network or simply due to leaks in bends and joins in the network. By deploying sensors to measure pressure prior to and after compression and at different stages in the network, we can easily identify unexpected and undesirable pressure drops and focus on quickly identifying and eliminating the root cause of the problem.
Temperature changes: We know from our high school science books that compressing the same amount of hot air is a lot more effort than when the air is colder. Similarly, temperature drops in compressed air adversely impact the air pressure. So it is important to maintain the optimal air temperature on either side of the compression exercise. Measuring, monitoring, and tightly controlling air temperature at intake and through the transmission process is important for the efficient use of the energy spent in compressing air.
Throttling & idle times: Ensuring that the right amount of compressed air at the right pressure is being delivered to the different end points, and only when needed ensures that we only spend as much energy as needed to compress the air.
By monitoring and measuring using strategically placed IoT sensors, tracking ongoing performance in real-time against benchmarked ideal-state KPIs, one can get better visibility into the performance of this equipment and the costs associated with running them. Now, Sensital also supports bidirectional communication between sensors, devices, and your IT systems. This means we can also automatically initiate control actions to adjust valves, actuators, coolants, lubricants, etc., or even initiate a trouble ticket for preventative maintenance. This allows you to not only measure and track, but also adjust and optimize in real-time, for true digital management of the performance of key supporting equipment and associated operational costs.