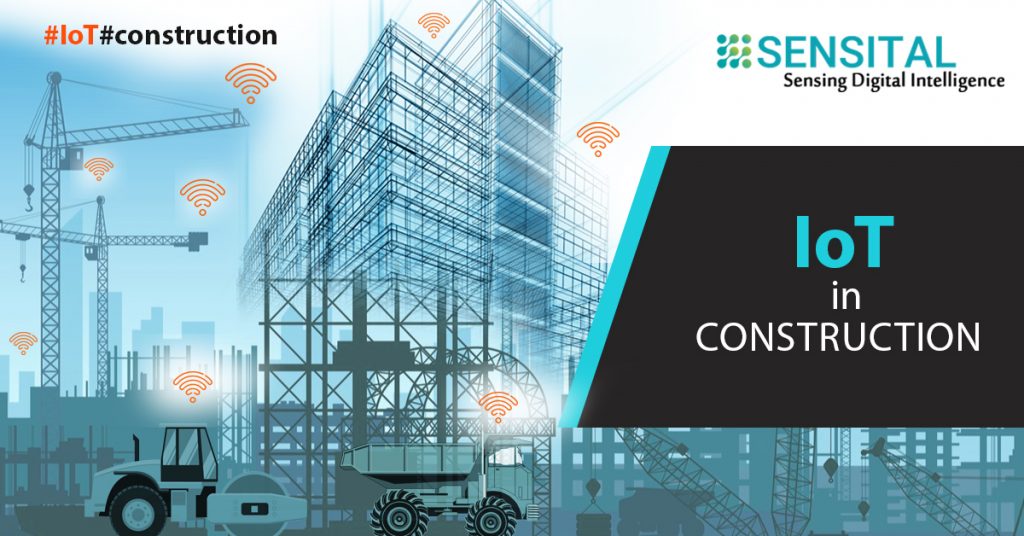
Proliferation of technologies like wireless networks and mobile smart devices has accelerated the urbanization of the world. This urbanization has initiated ancillary industrial construction initiatives building new like energy grids, power plants, factories, etc. and modernization with intelligent buildings and smart infrastructures. While the global construction industry is expected to continue this trend and grow to about $13T by 2023 and about $20T in the next 15 years, the productivity growth hasn’t kept up with this explosion in the global construction market. In fact, with an average of 1% annual productivity growth, Construction lags behind practically all major industries in improvements in productivity.
There are a few challenges faced by the construction industry either during the project execution or post-delivery management. However, with less than a third of all construction projects coming within 10% of the projected budget, construction project cost over-runs are a big problem in the industry. There are other challenges the construction industry has to cope with as well, including safety & security, energy management, waste management, etc.
Technology adoption in Construction
The tepid growth in productivity is also correlated to the slow adoption of technology in the construction industry. This also means that the opportunity to apply technological innovations is also significant in terms of tangible value addition.
KPIs and data driven project management would lead to improvements in productivity, costs, in time and within budget project delivery, workforce safety and stronger compliance with OH&S regulations. Enabling access to this data in real time, feeding the right operational information into the project planning and management with true IT-OT integration is how IoT can help improve operational efficiency and reduce financial over-runs in construction projects.
Also, appropriate technology adoption will also contribute to other key facets such as increased productivity & efficiency in on-going Facilities management, meeting SLA’s with reduced crisis management and enhanced customer experience.
Applications of IoT in Construction
There are a number of proven ways, borrowed from other Industry 4.0 applications, in which IoT can be applied to the Construction industry in general and specifically in the two key areas of productivity and cost control.
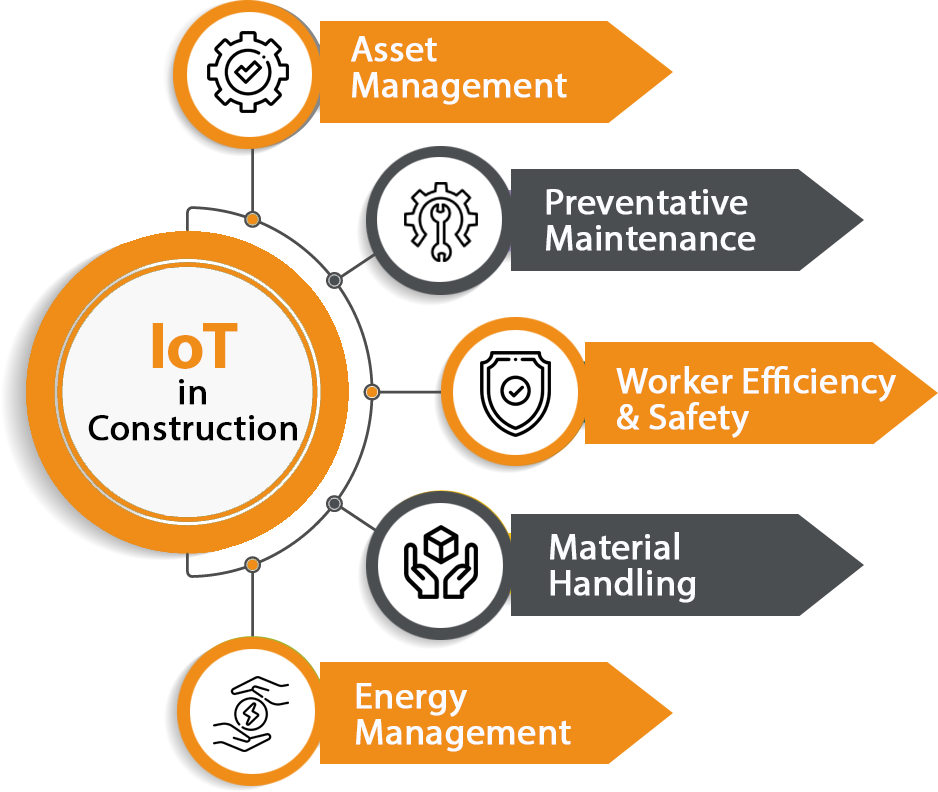
Asset management – With a variety of sensors, devices and a platform to enable bidirectional information flow, IoT can help track capital assets and ensure that they are available at the right location at the right time.
Preventative maintenance – By IoT based real-time monitoring and tracking the health of key machinery, equipment, HVAC systems, energy and power sources, initiating preventative maintenance and ensuring that these assets do not fail unexpectedly, project delays and expensive repairs can be avoided.
Worker efficiency & safety – Tracking worker location and movements across the construction site and facilitating workers’ direction to the right place and at the right time will ensure that construction employees are efficient and effective. Detecting any hazardous condition (ambient, environmental or equipment related), tracking workers and initiating timely evacuation can ensure that employees are moved to safety quickly.
Material handling – Monitoring raw material consumption, automated initiation of replenishment via integration with ERP systems and tracking material movement throughout the supply-chain will ensure optimal material availability, limit wastage and reduce inventory costs.
Energy Management – IoT based distributed energy resource management can ensure timely and optimal power supply, react to surges in power demand or shutting down power when not needed, all leading to lower energy costs and minimal power wastage.
Beyond project implementation productivity and cost management, these applications of IoT can also help with efficient operations management and maintenance cost controls in the post construction management of the asset. Some such examples include:
- Ambient condition monitoring – Ensuring that the temperature levels are maintained in each part of the facility, especially for areas that require strict temperature and moisture controls (data centers, storage areas, conference rooms, etc.) and automatically adjusting temperature and moisture levels. We can take this one level further with also making sure that the HVAC systems are functioning properly through timely preventative maintenance will ensure proper ambient condition in key areas of the facility.
- Efficient energy management – Managing the demand and supply of energy based on power consumption peaks and valleys, introducing alternate power sources or giving energy back to the grid can lead to a NetZero operation of the facility.
- Safety & security – Monitoring and controlling access controls to various parts of the facility, tracking assets and movement of assets in and out of the facility, as well as within it and ensuring we have the right kind of approved people or equipment in the right areas of the facility with real-time IoT based tracking.
Overall Project Health Visibility
All the areas of improvements listed above are important and lead to savings, but any one of them, in itself or not in conjunction with the others will still lead to overall inefficiencies. Access to data across the whole project and the ability to react to information change in any area in real time means that smart decisions against KPIs can be made in a timely manner. True IT-OT integration facilitated by an IoT platform that supports interoperability and communication between a variety of sensors, devices, data formats and protocols enables that real-time information flow across the whole construction project and these different silos to give that single pane of view for the overall health of the entire project.